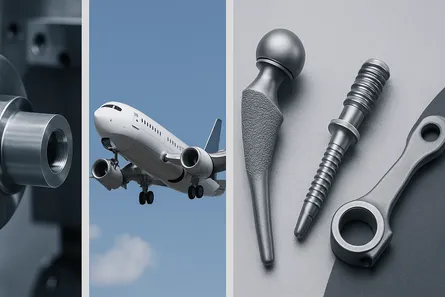
Why Titanium Is Taking Over Modern Manufacturing: Strength, Lightness, and Beyond
Titanium is no longer just a metal for fighter jets and surgical tools—it's becoming a cornerstone of modern manufacturing. As industries seek materials that are strong, lightweight, and resistant to extreme conditions, titanium’s unique properties are turning it into a go-to solution across sectors. From aerospace engineering to medical implants, this wonder metal is proving it has what it takes to meet 21st-century demands. This article takes a close look at the rise of titanium in modern manufacturing: its advantages, applications, the challenges of working with it, and where this trend is heading next.Why Titanium? The Material That’s Changing the Game 1. Strength Without the Weight Titanium has an extraordinary strength-to-weight ratio, offering the durability of steel at almost half the weight. That’s a major advantage in industries like aviation and automotive, where every kilogram matters. 2. Resists the Harshest Environments Unlike many metals, titanium doesn’t corrode easily—even when exposed to saltwater, industrial chemicals, or high heat. Ideal for chemical plants, offshore equipment, and high-performance engines. Naturally forms an oxide layer that protects it from rust and degradation.3. Compatible with the Human Body Titanium is non-toxic and biocompatible, which is why it’s used in medical implants ranging from dental screws to spinal plates. It doesn’t trigger immune reactions and integrates well with bone and tissue.Where Titanium Is Making an Impact 1. Aerospace EngineeringTitanium parts are standard in jet engines, airframes, and landing gear. Alloys like Ti-6Al-4V are used for their heat resistance and structural reliability. Leading manufacturers like Boeing and Airbus now rely heavily on titanium to reduce weight and improve fuel efficiency.2. Medical Devices and ImplantsUsed in hip replacements, pacemaker cases, and bone screws. 3D printing allows for patient-specific implants with faster recovery and better fit. Titanium’s biocompatibility ensures long-term success with minimal complications.3. Automotive and MotorsportsLuxury and electric vehicle makers are adopting titanium for suspension systems, exhausts, and even brake components. Reduces vehicle weight while improving durability and thermal stability.4. Industrial Machinery and ToolingTitanium heat exchangers, pumps, and valves are used in harsh environments like desalination plants and acid-processing facilities. In manufacturing, titanium components last longer and reduce maintenance costs.Challenges in Working with Titanium 1. Difficult to Machine Titanium is hard on tools and dissipates heat slowly. That means: Slow cutting speeds Frequent tool changes Advanced cooling and coatings needed2. Welding and Fabrication Complexities Titanium reacts quickly with oxygen at high temperatures, which can weaken welds. Requires argon shielding or vacuum chambers. Laser and electron beam welding are becoming more common solutions.3. High Material Cost Refining titanium is energy-intensive, and raw titanium costs 3–6x more than aluminum or steel. However, its durability and lower lifecycle cost make it worthwhile for critical parts.Innovation Driving Titanium Adoption 1. Additive Manufacturing (3D Printing)Titanium powders used in Direct Metal Laser Sintering (DMLS) and Electron Beam Melting (EBM). Allows complex part geometries, lightweight lattice structures, and rapid prototyping.2. Advanced AlloysNew blends improve machinability while retaining titanium’s key strengths. Ti-6Al-4V remains the most widely used, but other alloys are tailored for specific industries.3. Sustainability and RecyclingTitanium is highly recyclable with up to 95% material recovery. Manufacturers are increasingly turning to recycled titanium to reduce cost and carbon footprint.The Road Ahead for Titanium in Manufacturing 1. Growing Global DemandAerospace and medical sectors continue to drive demand. The titanium manufacturing market is expected to grow at a CAGR of 7.5% through 2030.2. Increased Use in Consumer ProductsTitanium is showing up in everything from smartphone frames to eyewear and watches, thanks to its sleek look and high durability.3. Cross-Industry CollaborationTitanium innovation is no longer siloed—automotive engineers are learning from aerospace welders, and medical researchers are leveraging 3D-printing techniques from industrial design.