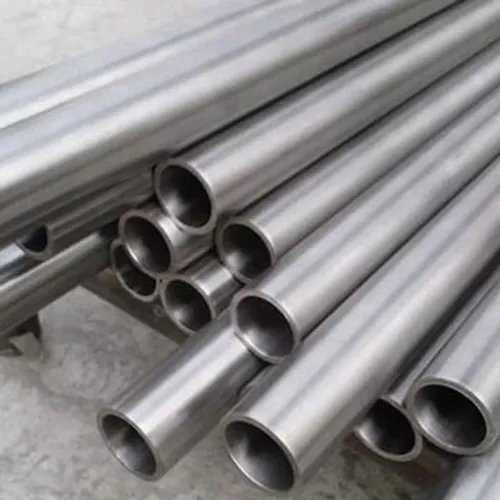
Mastering the Flow: Fabrication and Installation of Titanium Pipe Systems
A titanium piping system is an investment in long-term reliability. To realize its full benefits, proper fabrication and installation techniques are essential. The primary focus must always be on maintaining cleanliness and ensuring perfect inert gas shielding during welding.
1. Cutting and Bending
- Cutting: Titanium pipes can be cut using mechanical methods like abrasive cutters or band saws. The key is to use sharp blades and low speeds with coolant to prevent overheating and contamination.
- Bending: Due to titanium’s springback, pipes must be bent past the target angle. Cold bending on a mandrel bender is common for standard grades like Grade 2. Stronger alloys may require warm bending to prevent cracking. Always use clean tooling.
2. The Art of Welding Titanium Pipes
Orbital TIG (GTAW) welding is the preferred method for consistency, but manual welding is also common. Success depends entirely on shielding.
- Meticulous Cleaning: Before welding, the pipe ends must be thoroughly degreased with a solvent like acetone. The welder’s gloves must be clean.
- The Shielding Trifecta: To prevent atmospheric contamination, three zones must be protected with Argon gas:
- Primary Shielding: From the welding torch itself.
- Trailing Shielding: A trailing shield cup that follows the torch to protect the hot weld bead as it cools.
- Internal Purging (The Most Critical Step): The inside of the pipe must be purged of all oxygen. This is done by sealing the pipe ends with dams (tape or plugs) and filling the interior with Argon before and during welding.
3. Weld Inspection and Quality Control
- The Color Test: The color of the finished weld is a direct indicator of its quality. A shiny silver or light straw color is perfect. A blue color is acceptable but not ideal. Gray or white, powdery welds are heavily contaminated, brittle, and MUST be completely cut out and re-welded.
- Non-Destructive Testing (NDT): For critical applications, welds may be inspected using dye penetrant or radiographic (X-ray) testing to ensure they are free of cracks or porosity.
4. Assembly: Flanges and Fittings
- Flange Joints: The most common way to connect titanium pipes to equipment or other pipes. Weld-neck flanges are preferred for strength.
- Gaskets: Use gaskets made from materials compatible with the process fluid (e.g., PTFE/Teflon). Avoid graphite-impregnated gaskets which can cause issues.
- Bolt and Nut Material: To prevent galvanic corrosion, use compatible fasteners or isolate them properly.
By following these disciplined procedures, you ensure that your fabricated titanium pipe system will deliver the corrosion-free, long-lasting performance it was designed for.
Quick Contact
Related Products
-
Seamless vs. Welded: A Guide to Choosing Your Titanium Pipes
Titanium pipes
Product Categories
- Titanium Anode Basket 1
- Titanium Foils 1
- Titanium Pipes 1
- Titanium Rods 1
- Titanium Tubes 1
- Titanium Wires 3
- Nuts & Bolts 1
- Special Titanium Alloys 1
- Titanium Anodes & Electrodes 1
- Titanium Equipment 1
- Titanium Mesh 1
- Titanium Sheets & Plates 1
- Titanium rods 3
- Titanium foils 3
- Titanium sheets and plates 3
- Titanium pipes 3