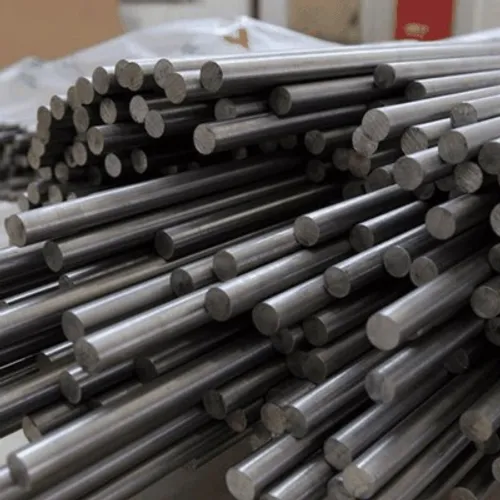
5 Essential Tips for Successfully Machining Titanium Rods
Titanium has a well-deserved reputation for being challenging to machine. However, “challenging” does not mean “impossible.” The difficulties arise from titanium’s unique physical properties: its low thermal conductivity, high chemical reactivity, and low modulus of elasticity.
By understanding and respecting these properties, any competent machine shop can achieve excellent results. Here are five essential tips for successfully machining titanium rods.
1. Keep It Cool: Flood with High-Pressure Coolant
Heat is the number one enemy when machining titanium. Unlike steel, titanium is a poor thermal conductor, meaning heat doesn’t flow away from the cutting edge. Instead, it concentrates on the tool and the workpiece surface, which can rapidly destroy the cutting tool.
The Solution: Use a high-pressure, high-volume flood of coolant directed precisely at the cutting edge. The goal is twofold: to cool the tool and workpiece, and to aggressively flush chips away from the cutting zone before they can cause more problems.
2. Slow and Steady: Low Cutting Speeds, High Feed Rates
This is the golden rule of titanium machining. It may seem counterintuitive, but high cutting speeds are a recipe for disaster. High RPMs generate excessive heat, causing the titanium to react with and weld itself to the cutting tool, leading to immediate failure.
The Solution: Program low surface speeds to keep heat generation to a minimum. At the same time, use a high and consistent feed rate. A high feed ensures the tool is always taking a substantial “bite” out of the material, which helps carry heat away with the chip. It also prevents the tool from simply rubbing against the workpiece, which generates friction and hardens the surface.
3. Rigidity is King: Eliminate Vibration
Titanium has a low modulus of elasticity, which means it tends to flex and push away from the cutting tool more than steel does. This can lead to vibration and “chatter,” which is detrimental to tool life and surface finish.
The Solution: Create the most rigid setup possible.
- Use the shortest, most stout tool holders and cutting tools available.
- Grip the titanium rod securely and as close to the machining zone as possible.
- Ensure the machine tool itself is robust and well-maintained.
4. Never Stop Cutting: Avoid Dwelling
A “dwell” occurs when a spinning cutting tool remains in one place without advancing into the material. When this happens on titanium, the friction instantly generates immense heat, work-hardening the surface in that spot and often galling the tool. This hardened spot will be extremely difficult to re-engage.
The Solution: Program toolpaths that ensure the tool is always moving and cutting. When a cut is finished, the tool should be programmed to retract away from the surface immediately, not linger.
5. Use Sharp, High-Quality Tools
Machining titanium is not the place to try and save money with cheap cutting tools. A dull tool will not cut effectively; it will plow and rub, increasing cutting forces and heat.
The Solution: Start with a sharp, premium-grade carbide tool, often one specifically designed with a geometry for titanium. Monitor tool wear closely and change inserts or tools at the first sign of dulling—don’t wait for them to fail completely. A small investment in fresh tooling will save you from scrapping an expensive piece of titanium rod.
By following these five principles, you can turn a notoriously difficult job into a predictable and successful manufacturing process.
Quick Contact
Related Products
-
The Top Industrial Applications of Titanium Rods
Titanium rods
Product Categories
- Titanium Anode Basket 1
- Titanium Foils 1
- Titanium Pipes 1
- Titanium Rods 1
- Titanium Tubes 1
- Titanium Wires 3
- Nuts & Bolts 1
- Special Titanium Alloys 1
- Titanium Anodes & Electrodes 1
- Titanium Equipment 1
- Titanium Mesh 1
- Titanium Sheets & Plates 1
- Titanium rods 3
- Titanium foils 3
- Titanium sheets and plates 3
- Titanium pipes 3