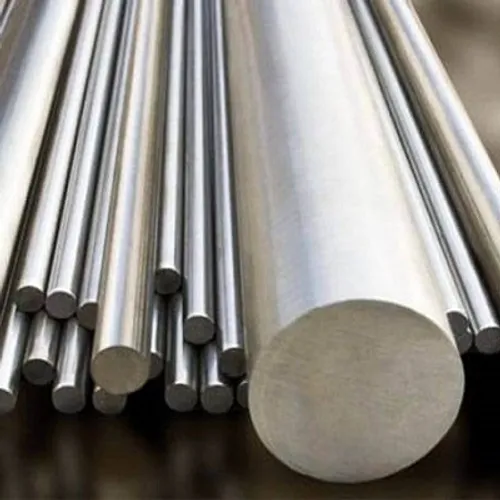
Choosing the Right Grade of Titanium Rod: A Guide for Engineers
When an engineer specifies a “titanium rod,” they are referring to a family of materials, not a single product. The choice between a commercially pure (CP) grade and a high-strength alloy is one of the most critical decisions in the design process. Selecting the correct grade ensures optimal performance, safety, and cost-effectiveness. This guide breaks down the key differences to help you make an informed decision.
The Foundation: Commercially Pure (CP) Grades
Commercially Pure titanium rods are over 99% titanium and are prized for one primary reason: unmatched corrosion resistance. They are softer and have lower tensile strength than alloys, but their formability and weldability are excellent.
-
Grade 2 (The Workhorse): This is the most common CP grade used for rods. It offers the best all-around balance of moderate strength, excellent formability, and superior corrosion resistance.
- When to Choose It: Select Grade 2 rods for applications where corrosion is the main enemy. Think pump shafts in chemical plants, valve bodies handling seawater, fasteners for marine equipment, or racks for anodizing lines. If the component will be constantly exposed to corrosive media and the mechanical loads are moderate, Grade 2 is your most reliable and cost-effective choice.
-
Grade 4 (The Strongest CP Grade): Grade 4 is significantly stronger than Grade 2 while retaining the same excellent corrosion resistance. However, this increased strength comes at the cost of reduced ductility, making it harder to form.
- When to Choose It: Opt for Grade 4 when you need the corrosion immunity of a CP grade but require higher strength than Grade 2 can offer, without moving to a full alloy. It’s often used for high-strength fasteners in marine environments or certain airframe components where corrosion is a major concern.
The High-Performer: Alloyed Titanium
Alloys are created by adding other elements—most commonly aluminum and vanadium—to the titanium base. This is done to dramatically enhance its mechanical properties, primarily its strength.
- Grade 5 (The Aerospace Champion - Ti-6Al-4V): This is the most widely used titanium alloy in the world, accounting for over 50% of all titanium usage. Its defining characteristic is an exceptional strength-to-weight ratio.
- When to Choose It: Grade 5 is the default choice for high-performance structural applications. If your primary goals are to reduce weight and maintain high strength, this is the grade you need. It is the backbone of the aerospace industry, used for landing gear, wing spars, and critical engine components. It’s also dominant in motorsport for parts like connecting rods and suspension components.
The Specialist: Medical Grade Titanium
Medical applications require a unique combination of strength, biocompatibility, and extreme damage tolerance.
- Grade 23 (The Implant Standard - Ti-6Al-4V ELI): Grade 23 has the same chemical composition as Grade 5, but with a crucial difference: it is an “ELI” (Extra Low Interstitial) grade. This means it has strictly controlled lower levels of oxygen, nitrogen, and carbon. These “interstitial” elements, while adding strength, can reduce the material’s ductility and fracture toughness.
- When to Choose It: Grade 23 is the gold standard for permanent medical implants. The lower interstitial content gives it superior fracture toughness, meaning it can resist cracking and failure even under immense, repeated stress inside the human body. This makes it the only choice for applications like hip and knee joint replacements, spinal fixation rods, and bone plates where reliability is a matter of life and death.
Quick Decision Guide
If your primary need is… | The best choice is… |
---|---|
Corrosion Resistance | Grade 2 |
High Strength-to-Weight Ratio | Grade 5 |
Medical Implants | Grade 23 |
Quick Contact
Related Products
-
The Top Industrial Applications of Titanium Rods
Titanium rods
Product Categories
- Titanium Anode Basket 1
- Titanium Foils 1
- Titanium Pipes 1
- Titanium Rods 1
- Titanium Tubes 1
- Titanium Wires 3
- Nuts & Bolts 1
- Special Titanium Alloys 1
- Titanium Anodes & Electrodes 1
- Titanium Equipment 1
- Titanium Mesh 1
- Titanium Sheets & Plates 1
- Titanium rods 3
- Titanium foils 3
- Titanium sheets and plates 3
- Titanium pipes 3