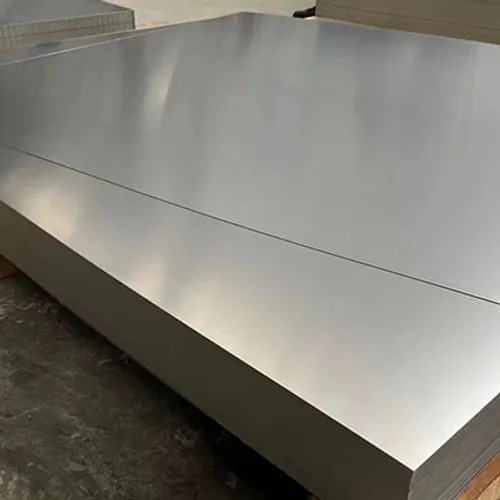
Fabricating with Titanium Sheets and Plates: Cutting, Forming, and Welding
Successfully fabricating parts from titanium sheets and plates requires an understanding of its unique properties. While not difficult, it demands specific techniques, especially regarding heat and contamination. Here’s a practical guide to the three key fabrication processes.
1. Cutting Titanium Sheet and Plate
Choosing the right cutting method depends on thickness, required precision, and budget.
- Waterjet Cutting: This is the preferred method for high precision. It cuts without heat, creating no Heat-Affected Zone (HAZ) and leaving a clean, smooth edge. Ideal for complex shapes and thick plates.
- Laser and Plasma Cutting: Faster and more cost-effective for large-scale cutting. However, they create a HAZ, which may require secondary machining to remove. Shielding gas is crucial to prevent edge contamination.
- Shearing: A mechanical method suitable for straight-line cuts on thinner titanium sheets (typically up to 4-5 mm).
2. Forming and Bending
Titanium has higher strength and more “springback” than steel, which must be accounted for during forming.
- Bend Radii: Titanium requires a more generous bend radius than steel or aluminum to prevent cracking. Stronger alloys like Grade 5 require a significantly larger radius than ductile grades like Grade 2.
- Cold vs. Hot Forming: Most forming of Grade 2 sheets can be done cold. For complex shapes or for forming stronger alloys like Grade 5, “warm” or “hot” forming (heating the material to 200-300°C or higher) may be necessary to increase ductility and reduce springback.
- Cleanliness: Tooling and dies must be impeccably clean to prevent iron contamination, which can compromise the titanium’s corrosion resistance.
3. Welding Titanium Sheet and Plate
Welding is perhaps the most critical fabrication step. The key to success is absolute protection from the atmosphere.
- TIG/GTAW Welding: This is the most common and reliable method. It offers excellent control over the weld pool.
- Absolute Gas Shielding: The molten weld puddle and the cooling metal must be shielded by an inert gas (usually Argon) until they are below ~425°C (800°F). This requires:
- Gas flow through the TIG torch.
- A “trailing shield” that follows the torch to protect the cooling weld bead.
- “Back-purging” gas on the reverse side of the weld.
- Weld Color is a Quality Indicator: A successful weld will be bright silver or a light straw color. Blue, gray, or white powdery colors indicate oxygen contamination and a brittle, failed weld that must be completely removed.
Success Through Proper Technique: Fabricating with titanium sheets and plates is straightforward when the right procedures are followed. By managing heat, preventing contamination, and respecting the material’s properties, you can create components with the legendary performance and longevity of titanium.
Quick Contact
Related Products
-
The Building Blocks of Engineering: Key Applications for Titanium Sheets and Plates
Titanium sheets and plates
-
Titanium Sheet vs. Plate: A Technical Guide to Selection
Titanium sheets and plates
Product Categories
- Titanium Anode Basket 1
- Titanium Foils 1
- Titanium Pipes 1
- Titanium Rods 1
- Titanium Tubes 1
- Titanium Wires 3
- Nuts & Bolts 1
- Special Titanium Alloys 1
- Titanium Anodes & Electrodes 1
- Titanium Equipment 1
- Titanium Mesh 1
- Titanium Sheets & Plates 1
- Titanium rods 3
- Titanium foils 3
- Titanium sheets and plates 3
- Titanium pipes 3