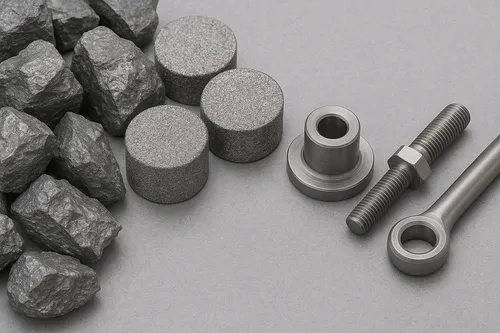
From Ore to Precision: How Titanium Parts Are Engineered for Excellence
Titanium parts used in aerospace, medical, and industrial systems don’t just start on a CNC lathe—they begin as minerals deep in the Earth. The journey from raw titanium ore to a precision-engineered component involves an intricate chain of metallurgy, chemistry, and machining expertise.
This article breaks down each step in the process: from extraction and refining to alloying, forming, and final finishing. Whether it’s a jet turbine blade or a spinal implant, the excellence of titanium parts lies in the science of their transformation.
Step 1: Extracting the Raw Material
Titanium is primarily extracted from ilmenite (FeTiO₃) and rutile (TiO₂) ores.
- Mining locations: Australia, South Africa, and Canada lead in titanium ore production.
- Once mined, the ore undergoes chlorination to produce titanium tetrachloride (TiCl₄), a volatile compound essential for purification.
Step 2: Refining via the Kroll Process
The Kroll Process remains the primary method for refining titanium:
- TiCl₄ is reduced using magnesium (Mg) in a high-temperature reactor.
- The result is a porous, sponge-like raw titanium—often called titanium sponge.
- This sponge is melted in a vacuum arc remelting furnace to produce ingots.
Though energy-intensive, the Kroll process produces high-purity titanium suitable for aerospace and medical applications.
Step 3: Alloying and Ingot Formation
Titanium is rarely used in pure form. It’s alloyed with elements like:
- Aluminum (Al) and Vanadium (V) for aerospace-grade materials (e.g., Ti-6Al-4V).
- Molybdenum (Mo) and Iron (Fe) for enhanced machinability and corrosion resistance.
These ingots are then forged or rolled into billets, slabs, or bars depending on their intended application.
Step 4: Forming and Machining
Precision forming techniques shape titanium into usable formats:
- Hot forging and extrusion shape structural parts.
- CNC machining refines parts down to micron-level tolerances.
- EDM (Electrical Discharge Machining) is used for complex geometries.
Because titanium has low thermal conductivity and high hardness, cutting requires slow speeds, rigid setups, and titanium-grade tool coatings.
Step 5: Surface Finishing and Inspection
Final steps involve enhancing performance and ensuring integrity:
- Anodizing or passivation creates a corrosion-resistant surface.
- Ultrasonic testing, X-ray diffraction, and dye penetrant inspection detect internal and surface defects.
- For medical and aerospace components, each part must pass strict ISO and ASTM standards.
Applications of Precision Titanium Components
- Jet turbine blades: High strength and heat resistance
- Dental and orthopedic implants: Bio-compatibility and non-reactivity
- Chemical valves and seals: Resistance to acid and salt corrosion
- Motorsport parts: Weight savings without compromising strength
Industry Outlook
With advancements in 3D printing, powder metallurgy, and AI-driven quality control, the engineering of titanium parts is becoming faster, cleaner, and more precise. As manufacturing pushes for lighter, stronger, and more sustainable materials, titanium’s role will only grow.