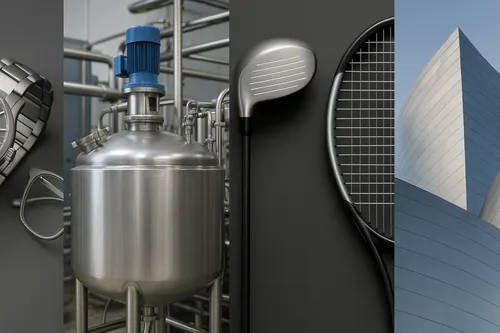
Surprising Industries That Rely on Titanium—and Why It’s Here to Stay
Titanium has long been associated with high-stakes industries like aerospace and medicine, but its unique properties are now being embraced in surprising new sectors. As engineers and designers search for materials that offer strength, longevity, and biocompatibility, titanium’s role is expanding far beyond what most people expect.
This article explores five unexpected industries that are leveraging titanium today—and why this metal is becoming indispensable across the board.
1. Fashion and Luxury Design
Yes, you read that right—titanium is trending in high-end fashion.
- Watches & Eyewear: Brands like TAG Heuer and Oakley use titanium for lightweight, scratch-resistant frames and casings.
- Jewelry: Hypoallergenic and corrosion-proof, titanium rings and bracelets are popular among people with sensitive skin.
Its minimalist aesthetic and resistance to wear make titanium a staple for modern luxury products.
2. Food Processing and Culinary Equipment
In commercial kitchens and industrial food plants, cleanliness and corrosion resistance are critical.
- Titanium knives and utensils stay sharp longer and resist food acids.
- Food-grade titanium tanks are used for brewing beer, fermenting dairy, and handling acidic products like vinegar or citrus juices.
Unlike stainless steel, titanium doesn’t leach metals under heat or acidic conditions, making it safer and longer-lasting in the food sector.
3. Sports and Recreation Equipment
While cycling and camping gear is already embracing titanium, other sports are catching on:
- Golf Clubs: Titanium driver heads offer better energy transfer and lighter swing weight.
- Tennis Rackets & Hockey Sticks: Titanium-reinforced frames improve strength without compromising flexibility.
- Diving Gear: Titanium dive knives and regulators resist saltwater corrosion better than steel.
For performance-focused athletes, titanium offers a competitive edge.
4. Chemical and Pharmaceutical Industries
In labs and factories that process corrosive chemicals, titanium provides unmatched resistance.
- Titanium reactors and piping are used in the production of drugs, acids, and petrochemicals.
- Unlike other metals, titanium won’t contaminate sensitive chemical mixtures or break down over time.
Its reliability reduces maintenance cycles, making it a cost-effective long-term choice for manufacturers.
5. Architecture and Building Materials
Architects are using titanium for more than just cladding:
- Roof panels, window frames, and structural supports made from titanium alloys are now being used in landmark buildings.
- The metal’s natural oxide layer forms a self-healing surface, making it weather-resistant for decades without repainting.
Examples include the Guggenheim Museum Bilbao, whose shimmering titanium facade has become iconic.
Why Titanium’s Popularity Will Keep Growing
- Recyclability: With a recovery rate of over 90%, titanium is one of the most sustainable metals in industrial use.
- Innovation in Manufacturing: Advances in 3D printing, powder metallurgy, and hybrid materials are lowering production costs.
- Consumer Awareness: People are becoming more conscious of quality, health, and environmental impact—areas where titanium excels.
Titanium’s combination of aesthetic appeal, strength, and versatility makes it not just a trend, but a foundational material for the future.